3.5 Vacuum Jet Dehydration

Vacuum Jet Dehydration Technology
Vacuum Jet Dehydration Technology has been invented by OilPure more than 25 years ago learning from the existing problems in Conventional Vacuum Distillation that can not ultimately solve water dehydration in oil. This Vacuum jet Dehydration technique has been a new theory of Non Vacuum for water removal in the oil.
Vacuum Jet Dehydration applies oil pressure at 70 psi and oil temperature at 140 °F mixing with atmospheric air to atomize through nozzle to create oil & water aerosol mixture, swinging through a cyclone separator.
The air/ oil mixing action forms the fluid mixture into aerosol as it enters the special design cyclonic separating tanks. At the right oil temperature any atmospheric air (even humid air) will increase its velocity while absorbing water from oil in the cyclonic separating tank. Water was previously in a liquid state, when it dissolves in the dirty oil. After the aerosol is mixed with air, water changes from liquid state to vapor state in the cyclonic separating tank. The cyclonic forced air will carry dissolved water to the upper steam and allow dried oil to fall to to the bottom.
Vacuum Jet Dehydration incorporates MS1 Moisture Sensor to control water dehydration process so water content from 2,000 – 10,000 ppm from incoming dirty oil will be removed down to 10-50 ppm before dried oil is discharged from Vacuum Jet Dehydrator.
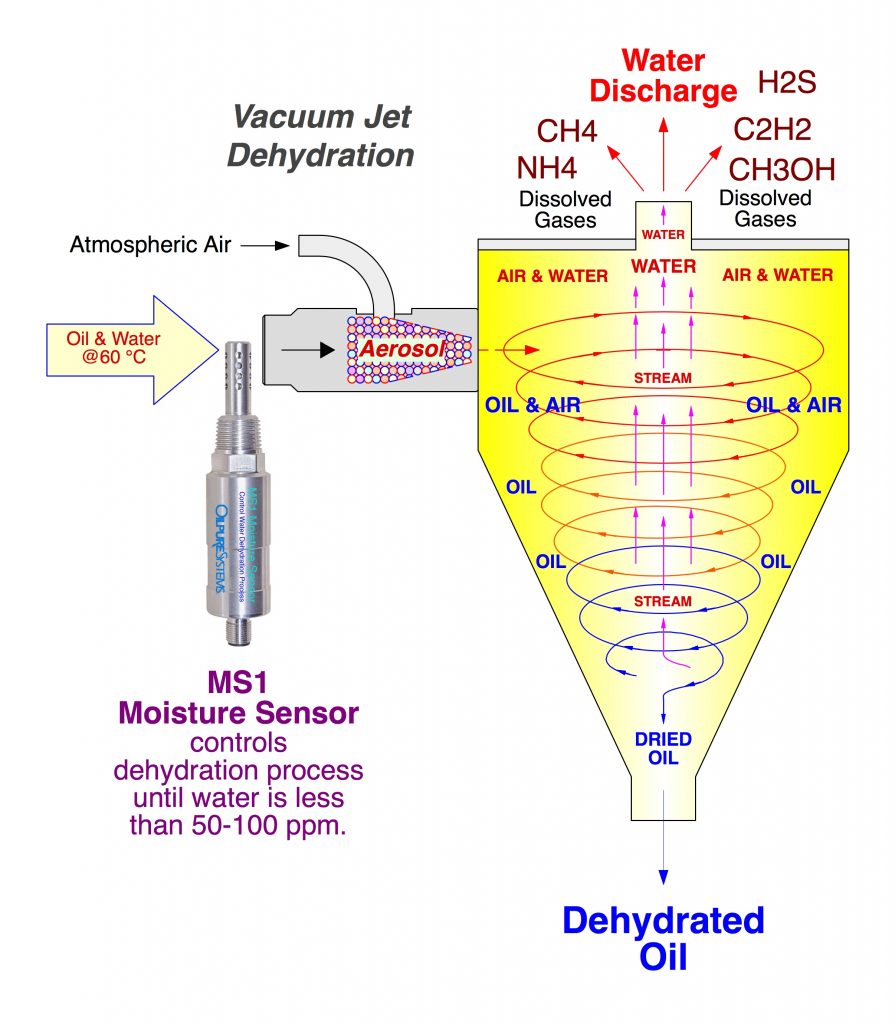
Vacuum Jet Technology is capable of not only removing Dissolved Water, but also removes Dissolved Gases that have decomposed in the lubricating oils.
MS1 Moisture Sensor is controlling the water dehydration process to assure that the incoming 2,000 – 10,000 ppm of water will be removed down to 10-50 ppm before the dried oil is discharged from the dehydrator.
Water changes from Liquid Stage into Vapor Stage at 140 °F during dehydration. This process saves heating energy for water dehydrating process
Dissolved Gases such as CH4OH Methanol in Biodiesel, CH4 Methane, C2H2 Acetylene, H2S Hydrogen Sulfide, NH4 Ammonia, CO2 Carbon Dioxide etc. will be atomized and inflated with dissolved water, rising from oil in the cyclone separator. NH4 Ammonia dissolved gas in refrigeration oil can be degassed by Vacuum Jet Dehydration as
Advantages of Vacuum Jet Dehydration Technology over Conventional Vacuum Technology:
- Vacuum Jet Dehydration can remove water from high viscosity gear oil up to 600 ISO grade viscosity while Vacuum distillation barely handle ISO 220 oil viscosity grade. Very little amount of water can be pulled out so it has to heat the oil temperature to 170°F – 175 °F to get more water out but risking the built up of Oil Oxidation and oil breakdown.
- When water content is over 3% (30,000) ppm of water in the oil reservoir, there will be excessive oil foaming occurred in the oil reservoir. This foaming will escape into vacuum pump and condenser causing vacuum pump premature damages and repair. So Vacuum Switch is energized to reduce vacuum level from 21-24 Inch/Hg down to 16-18 Inch/Hg in order to bring down excessive foaming in the vacuum chamber. This causes inefficiency in water removal for Vacuum Distillation. Most of the time this doesn’t work.
- Vacuum Jet Technology is also capable of degassing the Dissolved Gases such as CH3OH Methanol in Biodiesel, CH4 Methane, C2H2 Acetylene and H2S Hydrogen Sulfide in Transformer oil. Vacuum Jet atomizes these Dissolved Gases as well as water which has similar affinity to be ejected from cyclonic separator.
- Vacuum Distillation also removes these Corrosive Dissolved Gases through vacuum pump and condenser, causing component corrosion and premature failure to a short life vacuum pump.
- Vacuum Jet Dehydration is low or no maintenance using positive displacement gear pump to increase oil pressure. This gear pump has a 5 year MTBF (Mean Time Between Failure). Vacuum Jet Dehydrator is designed to run on a non stop 24 hours/ 365 days basis. Nozzle eductor in Vacuum Jet is a self cleaning and will automatically clean itself every 20 cycles. Therefore, there is no oil line clogging for m
- VJ-25 Machine. Good for oil reservoir size 100 – 150 gallons with water content of 5,000 – 10,000 ppm
- VJ-50 = VJ-50 + FC-1 Machine. Good for oil reservoir size 400 – 500 gallons with water content of 5,000 – 30,000 ppm
- VJ-100 = VJ-100 + FC-1 Machine. Good for oil reservoir size 750 – 1,000 gallons with water content of 5,000 – 30,000 ppm
- VJ-300 = VJ-300 + FC-4 Machine Machine. Good for oil reservoir size 1,500 – 2,000 gallons with water content of 5,000 – 30,000 ppm
- VJ-300DT = VJ-300 + FC-4 + DT-100 Machine. Good for oil reservoir size 2,000 – 2,500 gallons with water content of 5,000 – 100,000 ppm
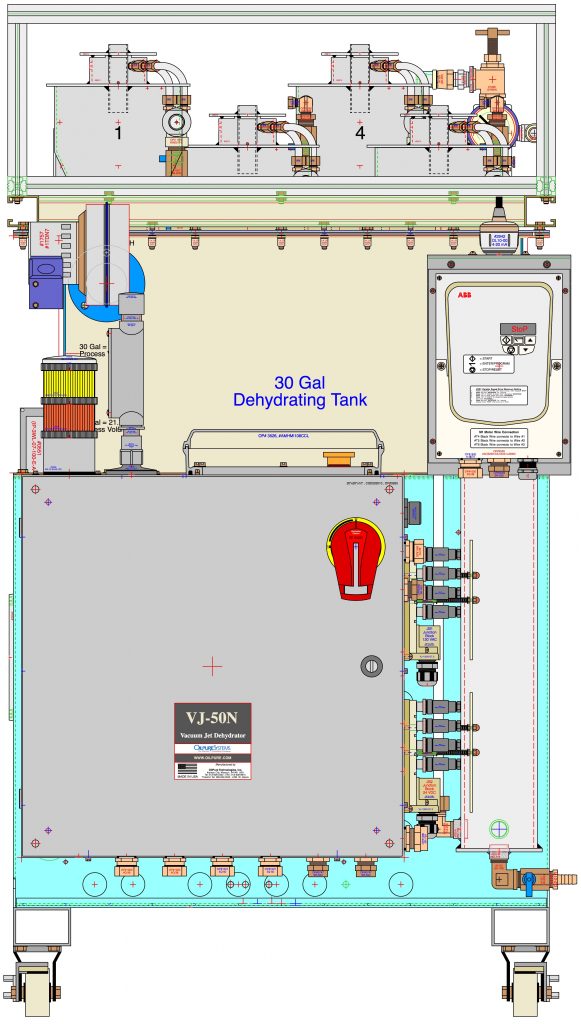
VJ-50 Vacuum Jet Dehydration
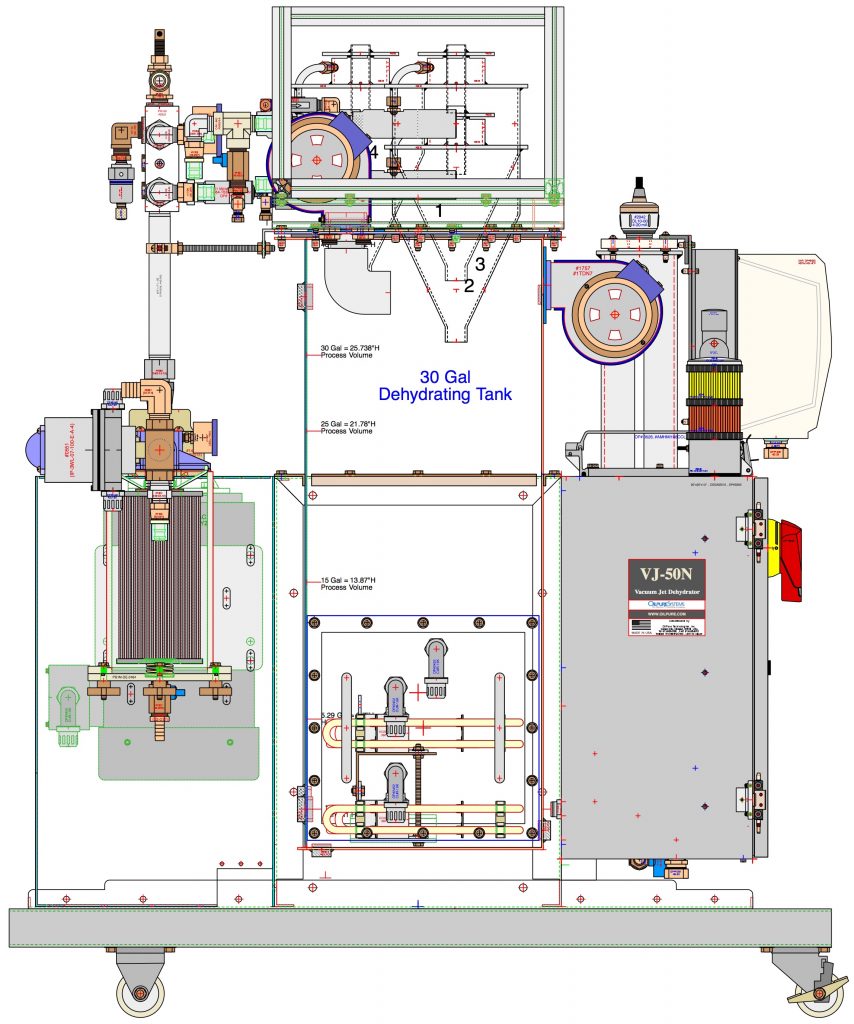
VJ-50 Vacuum Jet Dehydrator
VJ-50 Vacuum Jet Dehydration
Flow Capacity = 7 GPM Dehydrating flow rate with 22 GPM pump capacity.
- Capacity: 12 GPH per hour to remove 1% of water in oil.
- Oil Dialysis good for oil reservoir size 400-500 gallons or 1,600-2,000 liters
- Example of Oil Dialysis Time:
- 500 gal (2,000 liters) @ 1% Water = 500÷ 12 GPH
- = 41.6 hours x 3 passes = 125 hrs = 5 days
- Remove approximately 1/4 to 1/2 quart (400 cc) of dissolved water per hour. Water dehydration can be continuous or batch mode for more effective water removal.
- MS1 Moisture Sensor automatically controls water dehydrating time. The dehydrated discharge oil from VJ-50 will contain less than 100 ppm of water.
- Internal water dehydrating tank batch size is 30 gallons in the VJ-50 unit.
- Water starts to dehydrate at low oil temperature from 140 °F to 160 °F (60 °C to 71°C).
- Digital temperature control with high temperature alarm.
- 9.6 KW electric heater with 14 watts/sq. inch density.
- Water breakdown alarm when there is excessive water content in equipment oil reservoir.
- Variable Speed Drive (VSD) motor controls precision for oil flow and oil pressure.
- 3.5″ LCD digital touch screen display for operational messages with NEMA 4 enclosure
- Dry weight is about 300 pounds (140 kgs).
- Dimension 29″ W x 60″ L x 50″ H.
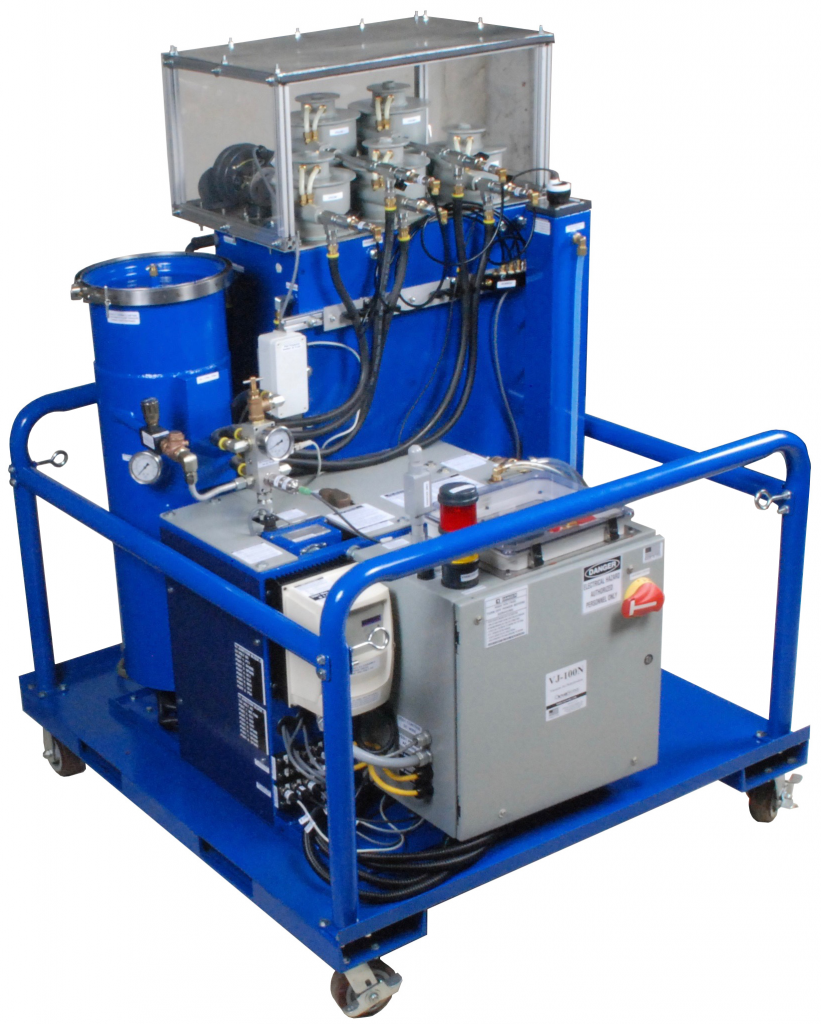
VJ-100 Vacuum Jet Dehydration
- 3.5″ LCD digital touch screen display for operational messages with NEMA 4 enclosure.
- Dry weight is about 700 pounds (320 kgs).
- Dimension 49″ W x 52″ L x 62″ H.
VJ-100 Vacuum Jet Dehydration
Flow Capacity = 9 GPM Dehydrating flow rate with 22 GPM pump capacity.
- Capacity: 15 GPH per hour to remove 1% of water in oil.
- Oil Dialysis good for oil reservoir size 500-1,500 gallons or 2,000-6,000 liters
- Example of Oil Dialysis Time:
- 1,000 gal (4,000 liters) @ 1% Water = 1,000÷ 15 GPH
- = 66.6 hours x 3 passes = 200 hrs = 8 days
- Remove approximately 1/4 to 1/2 quart (500 cc) of dissolved water per hour. Water dehydration can be continuous or batch mode for more effective water removal.
- MS1 Moisture Sensor automatically controls water dehydrating time. The dehydrated discharge oil from VJ-100 will contain less than 100 ppm of water.
- Internal water dehydrating tank batch size is 50 gallons in the VJ-100 unit.
- Water starts to dehydrate at low oil temperature from 140 °F to 160 °F (60 °C to 71°C).
- Digital temperature control with high temperature alarm.
- 9.6 KW electric heater with 14 watts/sq. inch density.
- Water breakdown alarm when there is excessive water content in equipment oil reservoir.
- Variable Speed Drive (VSD) motor controls precision for oil flow and oil pressure.
Previous Vacuum Jet Dehydrator in the Past
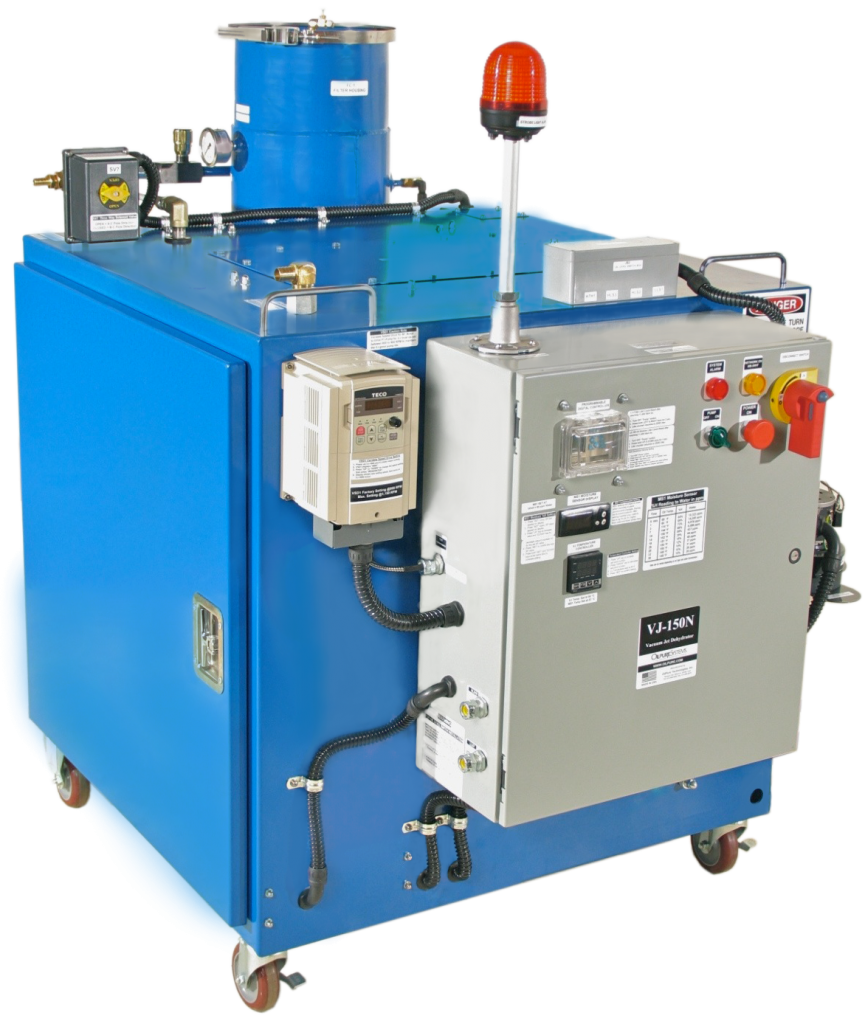
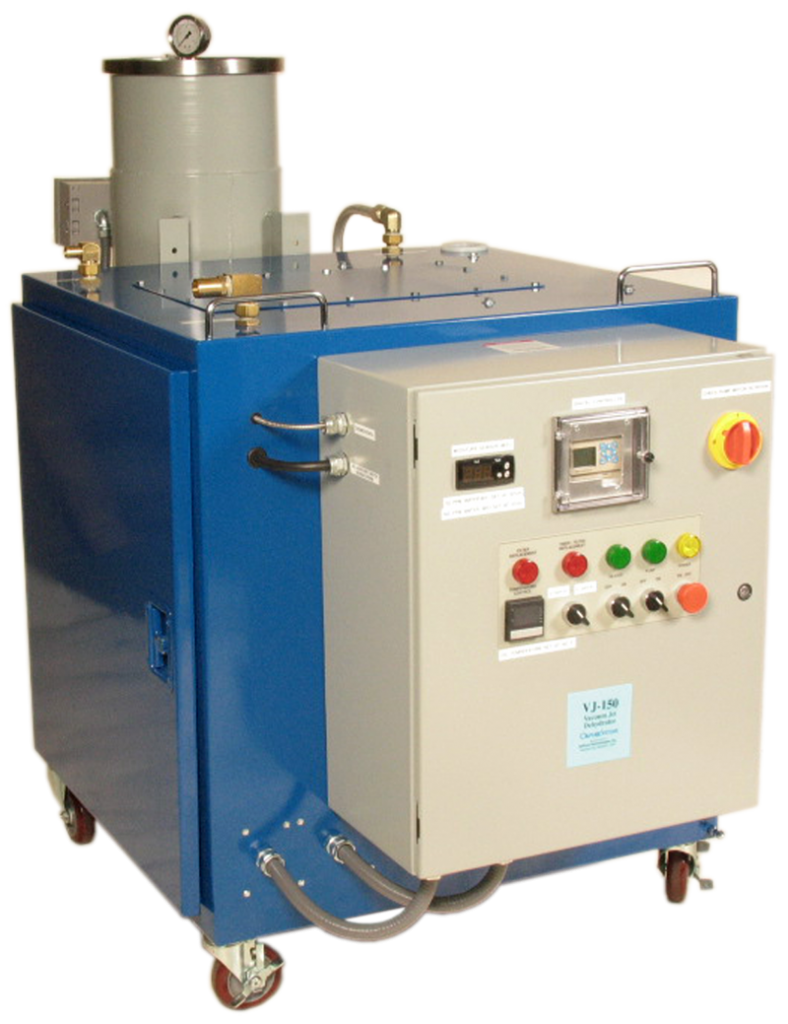
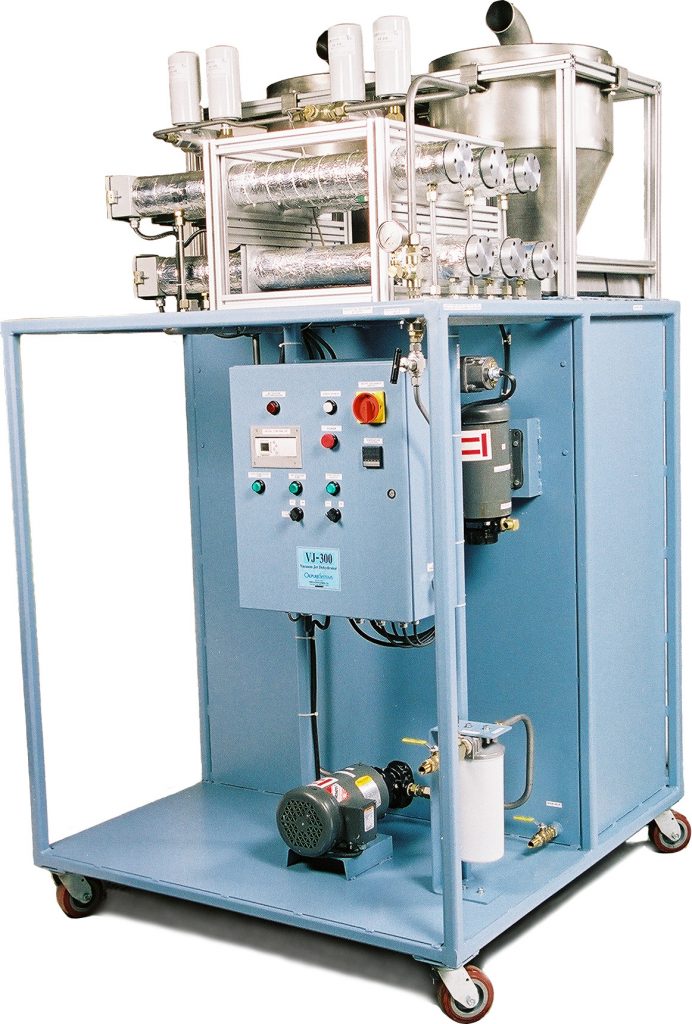
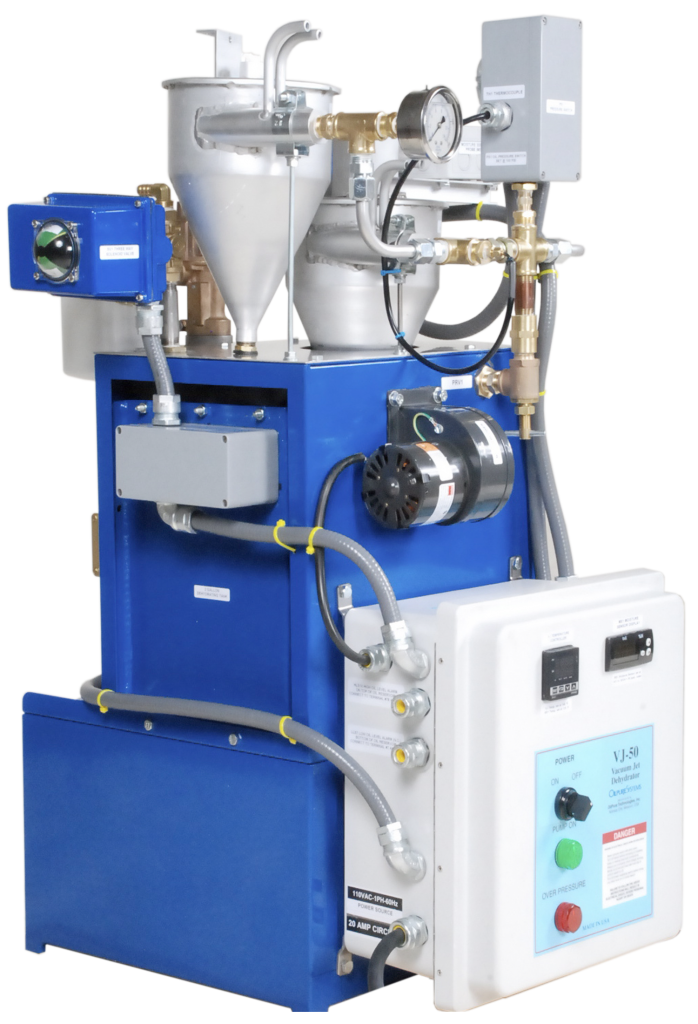
- Contact Information – OilPure Technologies, Inc.:
- P.O. Box 483976 • Kansas City • Missouri 64148 • USA • SKYPE ID: oilpure • LINE ID: oilpure
- Tel: 913-906-0400 • Mobile: 913-522-0272 • Fax: 913-906-9815
© Copyright, August , 2021
Document and information in this website is a proprietary information belonging to OilPure and is not allowed to reveal to public without OilPure consent.